DfMA: Why Manufacturing Is the Key to Viability – Blog 1: Introduction to DfMA and Its Core Principles
What would you say is the difference between manufacturing and construction? There are many ways to approach this question, but the simplest distinction is where the labor is performed. Manufacturing labor is performed in a factory, while construction labor is typically performed outdoors, in the elements. There are benefits, drawbacks, and limitations to each, and they are both essential for every construction project.
- Blog Post
- March 2023
- Pekka Moilanen
- Marketing Director
For decades, architects, engineers, and builders have been looking for ways to introduce the efficiencies of manufacturing into construction. In some circles, that effort is known as design for manufacturing and assembly (DfMA). Broadly, DfMA entails designing and manufacturing in a factory all the elements and components of a building, which are later to be assembled on-site. This approach offers tremendous benefits.
As ConstructionDive explains, DfMA enables spaces to be built more quickly at a lower cost while reducing the risk of project delays and minimizing on-site labor requirements. Based on these advantages alone, one might expect DfMA to become the default method of construction worldwide as architects, builders, and owners seek new efficiencies to offset labor shortages and rising material costs — but some concerns haven’t let that happen. Yet.
While there have been advances in recent years, the growth and adoption of DfMA has been characterized by some major setbacks. And I think the root of the problem has to do with manufacturing, more so than any other aspect of the process.
In this blog series, I will take a deep dive into DfMA to discuss its core elements, the benefits of DfMA, recent developments and setbacks, and the bright future that I think lies ahead for this ultra-efficient approach to construction.
In the coming blogs, I’ll discuss each of the following aspects of DfMA, starting with the basics:
DfMA 101
Centralized manufacturing and fabrication are at the core of the DfMA model. Rather than shipping materials to each job site, as is typically done with traditional construction (Figure 1), materials are shipped to centralized manufacturing facilities where building components are fabricated and then delivered to the job site for installation and assembly (Figure 2).
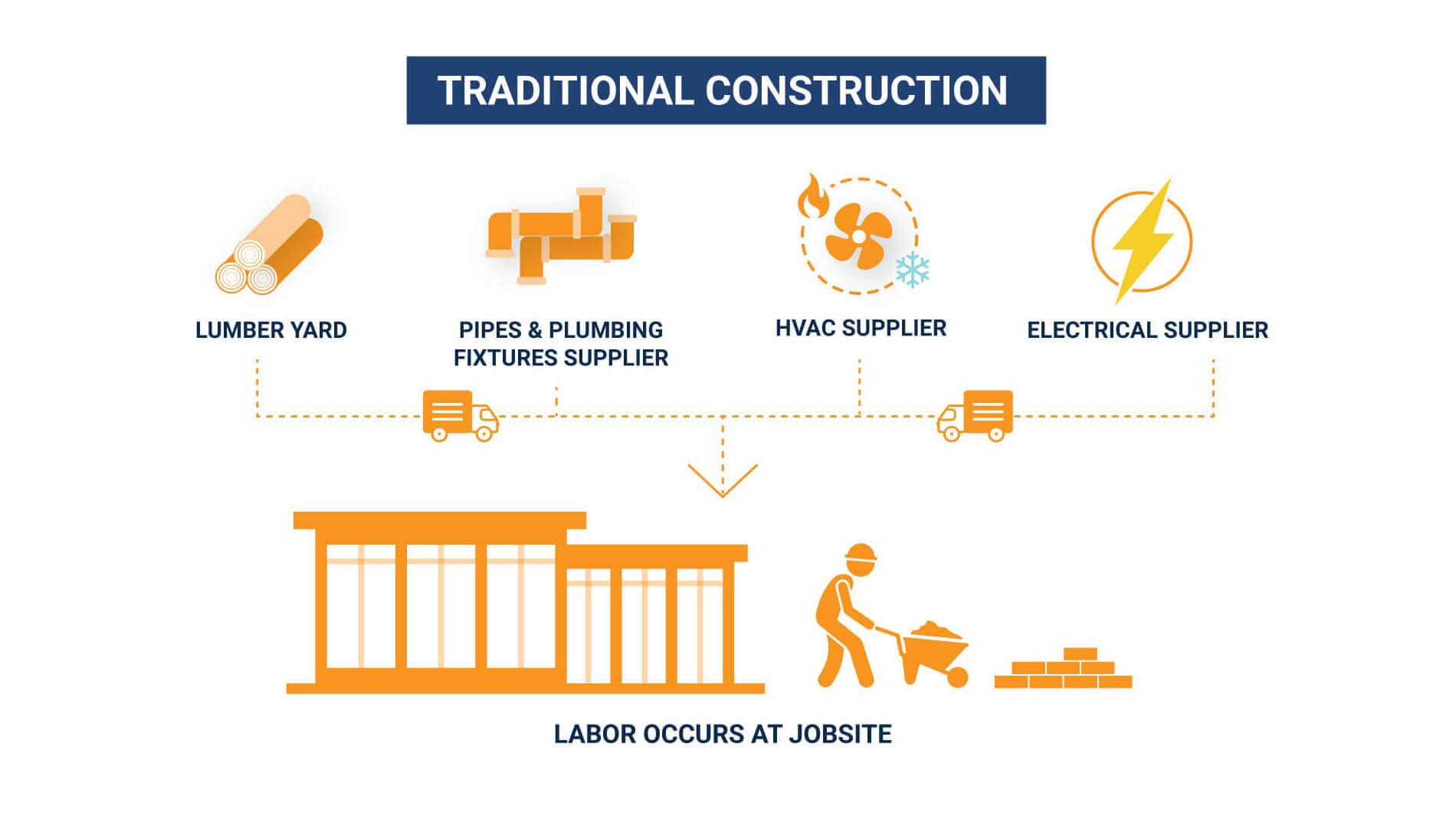
Figure 1: The traditional construction model.

Figure 2: The DfMA model.
While there are tremendous benefits to this approach, there are also challenges that the industry is still innovating to address — most notably, balancing the economics of manufacturing (based on economy of scale) with the unique environmental and project-specific challenges of every construction project.
Successful DfMA also depends on a high level of coordination between designers and all the trades working on each component of the structure. In this collaborative context, building information modeling (BIM) platforms such as Vertex BD are essential tools for smooth design, efficient fabrication, and well-organized installation at the job site.
Benefits of DfMA
The cost, efficiency, and environmental benefits of DfMA are similar to the benefits of off-site construction in general. However, these benefits are enhanced by the economies of scale that are made possible by the large-scale manufacturing, production, and supply chain optimization associated with DfMA.
For example, a factory specializing in panelized off-site construction can produce panels for a project in its climate-controlled facility to reduce waste, ensure quality, and accelerate the project’s schedule. However, if the architect for the project selected a standard wall panel that’s reproduced hundreds of times a day in another facility (rather than being custom built), additional savings would be realized.
DfMA reduces risk and waste by relying on mass-produced components fabricated in ideal conditions, and then passes those savings to builders and owners.
Recent Developments
The rise and fall of Katerra (the most ambitious DfMA startup ever launched) is the most important development in recent DfMA history. Founded in 2015, the startup spent more than $2 billion before going bankrupt in 2021. The company’s assets were later acquired by Volumetric Building Companies (VBC), which plans to produce several different building products in the acquired facilities.
Many important lessons can be learned from Katerra’s rapid growth and decline. Understanding what worked, what didn’t, and why the company failed are critical to moving DfMA forward in the coming years.
A Bright Future
We’ll conclude this series with a discussion about where DfMA is going and the factors that will make it an increasingly attractive option for architects and builders going forward. As markets around the world continue to struggle with housing shortages, climate change, and soaring raw material costs, DfMA is positioned to become a dominant trend in the not-too-distant future.
DfMA Will Revolutionize Construction
Perhaps the most important thing to understand about DfMA is that it is a trend that parallels and builds upon several other dominant trends in technology and industry:
- DfMA offers solutions that reduce building risks and costs.
- DfMA is more sustainable and less wasteful than traditional building processes.
- DfMA is technology-intensive and greatly benefits from increased adoption of BIM and design automation tools.
Over the coming months, I look forward to our discussion about DfMA and how it will reshape the global construction industry.
Related Stories
Best 3D construction software for professionals
Best 3D construction software for professionals 3D construction software has become a cornerstone of modern building projects, fundamentally transforming traditional construction practices. By enabling architects, engineers, and builders to create highly detailed,...
Leading construction design software for professionals
Leading construction design software for professionals In the ever-evolving construction industry, construction design software has become indispensable for streamlining workflows, enhancing accuracy, and improving collaboration. Among the available options, Vertex BD...
What is modular building design? – Unlock efficiency and precision
To fully unlock the potential of modular building design, it’s essential to utilize advanced tools that streamline the process from design to construction. While modular construction already offers significant advantages like faster timelines and cost savings, a tool like Vertex BD takes it further by integrating design and manufacturing into one seamless platform.