4 Steps to a Successful Off-site Construction Process
In our past blogs, we’ve described how off-site construction is an ideal option for many market applications worldwide. There are 5 crucial steps that need to be taken to make the construction process a success.
- Blog Post
- February 2021
- Pekka Moilanen
To recap, off-site construction is most beneficial in situations where:
- There is limited space for staging or storing construction materials on-site
- The building location is particularly remote
- The building will be assembled in extreme weather conditions
- Speedy completion of the structure is critical
- On-site safety and limited disturbance to the surrounding community is paramount
The advantages of off-site construction come with the building method itself. With permanent modular construction (or PMC), you build with modules, so you spend 90% of the pre-construction time in the design and submittal phase. Of the remaining 10%, up to 95% can be completed in a factory-controlled setting.
This makes the actual time on the job site extremely brief compared to traditional builds, but there are 5 crucial steps that need to be taken to make the construction process a success.
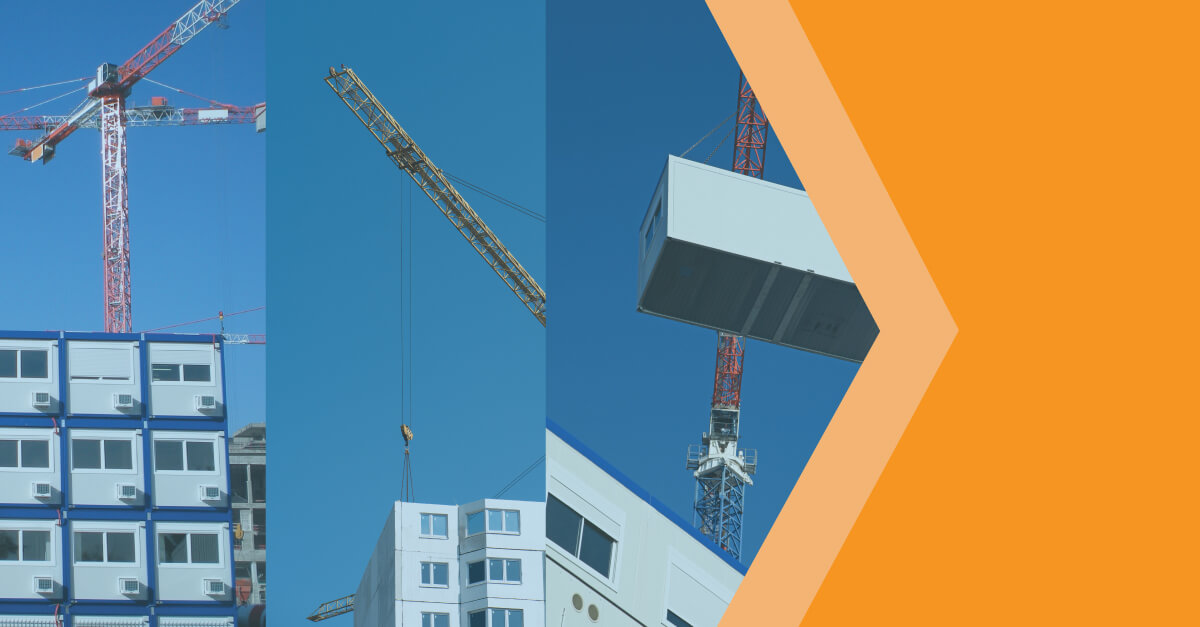
Step 1: Establish the Site
This is the one part of the construction timeline that doesn’t look much different than a traditional build.
During this step, grading and drainage is completed, as well as soil conditioning. This is also when the utilities are extended from the original access point to the connection to the building, including domestic and fire safety water, sanitary and storm sewers, gas, and electricity.
Step 2: Set the Foundation
With a modular build, the design of the foundation is dictated by the geo-technical investigation, the climate, and the modular plans themselves.
Modular buildings with floor assemblies may require a crawlspace, which will vary in size depending on the required under-floor access. Modular buildings without floor assemblies typically require a reinforced slab.
Just like traditional construction, there are different options for PMC attachments to foundation on-site, so the International Building Code is used to determine the construction type used for each building project. PMC may be constructed from hot-rolled steel, lightweight steel, precast, mass timber, or light-wood frames.
Step 3: Install the Crane
Almost all modular builds require a crane to lift and set the large, heavy modules. There are two methods that can be used for the lifting process:
- A spreader bar with belt strap to hold the modular box from underneath
- Pick points are connected to the corners of the module before being lifted
Either way, the lifting strategy needs to be decided on from the start, detailed in the plans for the modular structure, and engineered in a way that ensures a safe and level lift. All of this requires adequate manpower and precise scheduling.
The days when you’ll be lifting and placing the modules must be planned down to the minute. Access between the staging areas and crane lift points needs to be completely clear and, once the modules are placed, they need to be welded or bolted together and then attached to the foundation.
Step 4: Address the Building Envelope
Once the modules have been places and secured, infill sheathing is installed at all matelines (the joints between modules). There’s no sheathing in these areas, so the modules can properly attach to one another and create the appearance of a consistent façade from the exterior.
Installing a weather barrier around the building envelope is also critical to protect the modules. To do this, the install team and finishers work quickly to seam the roof, add water plans and wall cladding where required, and install a commercial front (if dictated in the design).
Once construction is complete, a final finish is applied to the building (the type of finish depends on the geographical region or building type), and you’re just a few steps away from finishing your project.
In our next blog, we’ll wrap up this series with everything you need to know to successfully finalize your off-site project.
To learn more about prefab building methods download our free eBook.
Related Stories
Best 3D construction software for professionals
Best 3D construction software for professionals 3D construction software has become a cornerstone of modern building projects, fundamentally transforming traditional construction practices. By enabling architects, engineers, and builders to create highly detailed,...
Leading construction design software for professionals
Leading construction design software for professionals In the ever-evolving construction industry, construction design software has become indispensable for streamlining workflows, enhancing accuracy, and improving collaboration. Among the available options, Vertex BD...
What is modular building design? – Unlock efficiency and precision
To fully unlock the potential of modular building design, it’s essential to utilize advanced tools that streamline the process from design to construction. While modular construction already offers significant advantages like faster timelines and cost savings, a tool like Vertex BD takes it further by integrating design and manufacturing into one seamless platform.