ACETRA Zwolle Project: Part Three
Project Location: Zwolle, the Netherlands
Project Date: Summer 2021
Working together with the entire design and construction team, Acetra advises the assembly of the three-story CLT structure to completion.
- Case Study
- Client: ACETRA
- Country: Serbia
- Type: CLT, Wood Framing, Residential & Commercial Construction
- Janko Maksimovic
Project Manager, Designer, Partner - Date: June 2022
With the design challenges addressed and the plans finalized, the Acetra team began preparing the build team for the unique process of assembling a CLT structure — but not without a few hiccups along the way.
Construction took place in the summer of 2021, so safety restrictions played a significant part in the build. Before COVID-19, the Acetra team would not be onsite 100% of the time but would make occasional visits to check on the teams’ progress and resolve any issues — visits that weren’t an option in early 2021.
“Because of the global pandemic, we weren’t allowed to visit the site,” explains Janko Maksimovic, project manager, designer, and partner at Acetra. “Still, we constantly communicated with the contractors and the assembly team to ensure that everything was put together properly and according to our design specifications.”
With all the communication done remotely, the Acetra team relied heavily on Building Information Modeling (BIM) technology, a tool that has streamlined the design and construction process in recent years. “These advancements in BIM technology have raised the industry to totally different levels,” says Maksimovic, explaining that the Vertex BD their team used allowed users to view the shared 3D model, click on any element, and instantly see all the properties, including material type, dimensions, and installation instructions.

“This feature is invaluable and means that each member of the design and construction team has access to every piece of information about the build, every step of the way,” Maksimovic explains. “Using this data, they can solve issues as they come up or give us a call and know we’re both working off the same precise plans to find a solution.”
Those precise instructions and level of communication are critical to the success of the build, as most of the assembly teams typically don’t have much experience with CLT construction. “Even if we provide drawings, details, and a visual representation of the assembly process, communication is still key,” says Maksimovic. “Not just because of the complicated assembly process, but if something happens, we need to provide a quick solution so construction can continue.”
Before the build team ever breaks ground or begins assembly, there is a lot of pre-planning to ensure the process is as smooth and seamless as possible.
“There are so many participants in these projects, from the architects to the electrical and plumbing contractors to the engineers and CLT producers,” says Maksimovic. “We all must work very closely together to create the best prefabricated solution for the specific site and building parameters. This way, with the addition of finished assembly drawings and the detailed 3D model, the assembly team is provided with everything they need to get to work and get the project done efficiently.”
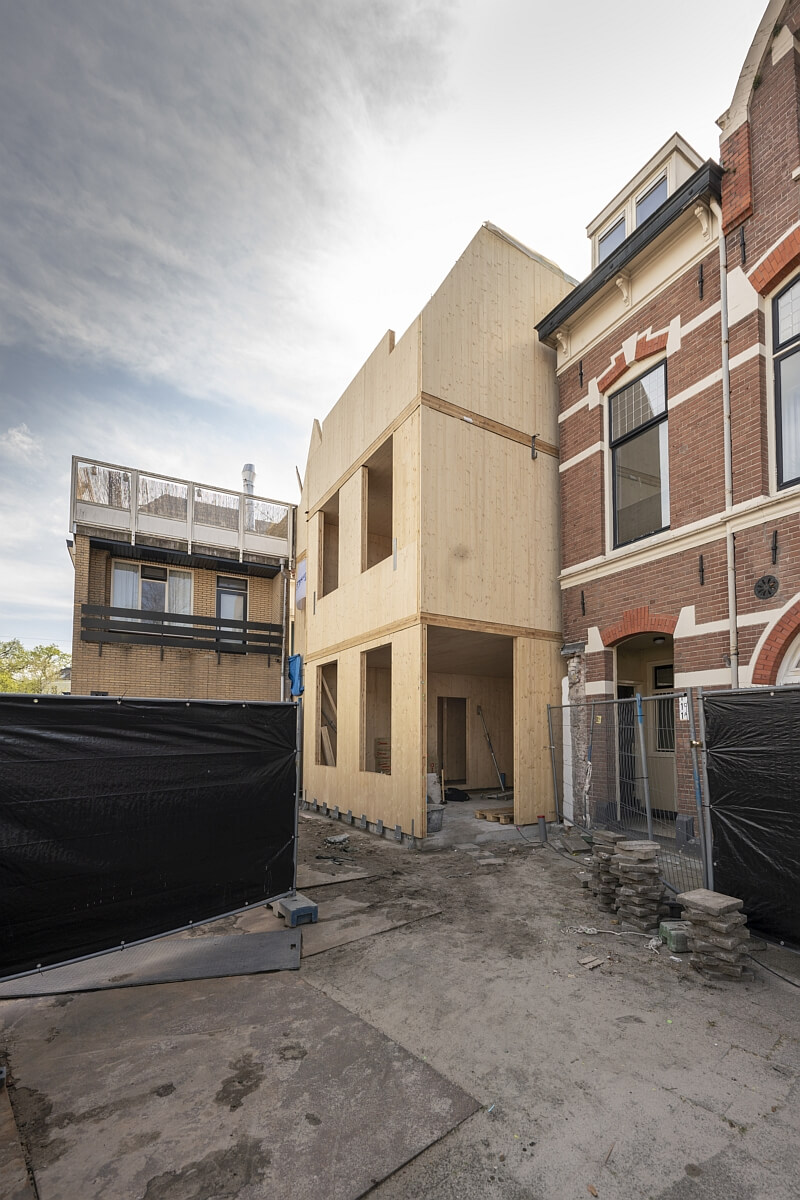
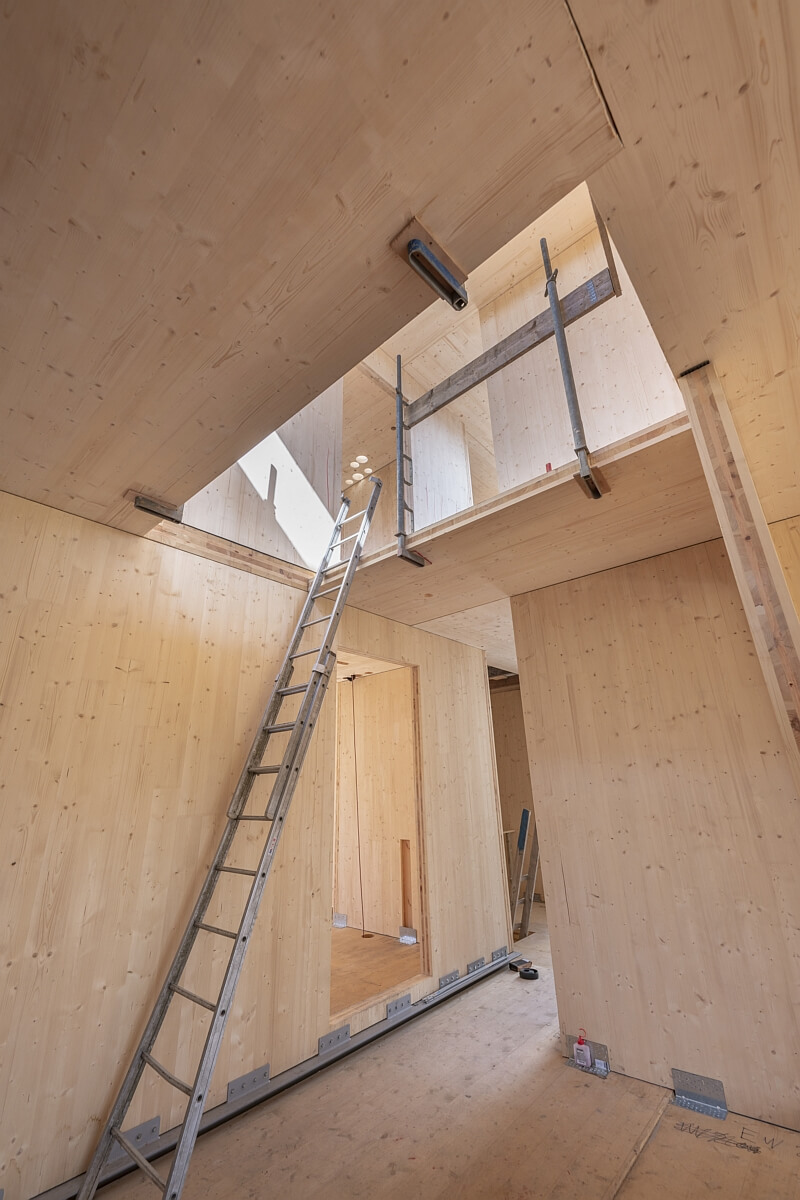
Calculating the Eco-Benefits of CLT Construction
At Acetra, they believe in the power and strength of mass timber — and all with a smaller environmental footprint than concrete. That’s why in each project they work on, they conduct a detailed analysis to calculate how much:
- Steel, timber, and connection elements are used for each CLT panel
- CO2 is emitted during the transport of building components to the construction site
- Waste is produced during the production of the panels and during construction
- Energy the building will use over the course of its lifetime
These numbers give a detailed look at the structure’s efficiency, both now and in the future, and provide the Acetra team with concrete data to improve their processes and stay committed to their goal of creating carbon negative buildings.
The Finished ZWOLLE Project: A Closer Look
Once construction began, it only took a couple of months to complete the three-story structure that stands between two existing buildings and features a total area of 789 m2.
Let’s take a closer look at the breakdown of the building:
Vertical elements include CLT walls and GL and steel columns. These elements take loads from horizontal building elements – CLT slabs and GL and steel beams.
Floors are made of heavy gravel and cement screed (a mixture of cement, aggregates, and water) over CLT slabs. This results in bigger dead loads (the weight of the building materials required to accommodate the construction of the project) but helps with the vibration of long single-span slabs.
CLT slabs are supported directly on the CLT walls or steel beams. The steel beams are hidden in floor layers and aligned on the bottom surface with visible CLT. Single-span beams are supported on 120×160 mm GL columns aligned with visible CLT walls. Most walls are 120 mm thick, but due to fire protection criteria, walls that are visible and exposed to fire from both sides are made of 160 mm thick CLT panels.
Horizontal stability is secured with external and internal CLT walls. Since the building is hidden and sheltered from most sides by other existing buildings, there are very few windows and doors. This means more elements that resist horizontal forces and smaller wind loads on the structure. As the building is in the Netherlands, there is almost no seismic activity.
Overall, the project was a great success and shows the benefits of combining CLT construction with shared technology for a smooth design and build process despite site challenges.
To learn more about Acetra and how they’re creating mass timber projects in an innovative, sustainable way, visit their website today.
Related stories
Helena Lidelöw: Steering VBC to global success with Vertex BD software
VBC grows with a core strategy centred on customisation and flexibility in Vertex BD, guided by Helena Lidelöw.
The three questions that shaped Ecohuis success in modular
Ecohuis, the leader in the Belgian modular home market, has shaped their success by focusing on three critical questions.
Leveraging automation: Vertex BD’s, Randek’s and Arcabo’s partnership offers unparalleled benefits
Arcabo has revolutionized home-building through strategic partnerships with Vertex Systems and Randek, leveraging automation to offer high-quality buildings at various price points.